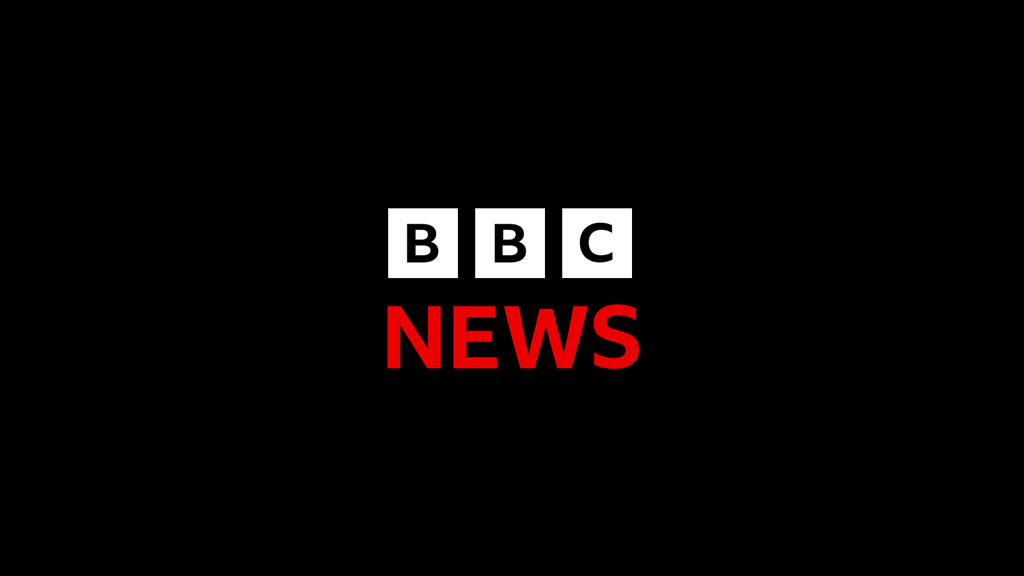
The production of spacecraft components while in orbit is closer to becoming a reality thanks to advancements in technology allowing for 3D printing in a weightless environment.
Dr. Gilles Bailet, from the University of Glasgow's James Watt School of Engineering, has been awarded a patent for a system for on-demand construction during space flight.
He hopes that this technology - which has been tested on a plane that operates in weightlessness - could make space exploration more environmentally friendly and help decrease the amount of space debris.
Dr. Bailet stated that his invention, utilizing granular materials, could facilitate the development of innovative equipment in space that could not be manufactured on Earth.
As the cost of launching objects into space continues to decline, we are witnessing an increasing number of things being sent into space, a trend that is hard to sustain.
Our concept is to be able to produce goods directly in space through 3D printing and, by doing this, we create opportunities for space-based recycling and establish a complete circular economic system.
The International Space Station (ISS) received its first 3D printer in 2014 and research on producing components outside Earth's gravitational influence has been ongoing since then, both on the ground and in orbit.
Dr. Bailet's prototype 3D printer utilizes a granular substance rather than the filaments commonly employed on Earth.
In spite of the challenges presented by zero gravity and the vacuum of space, the materials can be taken from a stock tank and transported to the printer's nozzle more quickly than other methods.
It was tested in November as part of the 85th parabolic flight campaign organized by the European Space Agency in partnership with Novespace in Bordeaux, France.
The team took their test kit on three flights, achieving more than 90 brief moments of weightlessness at the peak of sharp, rollercoaster-like ascents that were followed by rapid descents.
"Watching this technology work exactly as I envisioned it during the tests on a spacecraft was truly awe-inspiring, an overwhelming sense of various emotions," he said, alluding to the trials on the low-gravity plane - known as the "vomit comet" for its rollercoaster-like motion that creates 22 seconds of weightlessness every time it surges over a crest.
We are now confident that our technology functions effectively in a space environment, and we anticipate conducting the initial demonstration in space within the upcoming stage of our technological advancement.
Researchers Dr. Bailet and his team are also investigating ways to discreetly integrate electronic components into the materials during the printing process.
Presently, all objects entering Earth's orbit originate from the planet's surface and are launched into space via rocket propulsion.
The limitations on their mass and volume are rigid, and they can break apart violently during launch if their mechanical restrictions are exceeded, resulting in the loss of valuable cargo.
He pointed out that products created on Earth can be "less robust in the vacuum of space", and 3D printing has only been successfully conducted in the pressurised modules of the ISS so far.
While Dr. Bailet's project is currently developing components to augment spacecraft, such as radiators and antennas, it is anticipated that equipment could eventually be constructed in orbit.
These could include solar reflectors to generate zero-carbon electricity for transmission back to Earth, upgraded communication antennas, or medicinal research labs that can produce purer, more effective drugs.
"Crystals created in space tend to be larger and more symmetrical than those grown on Earth, making it possible for orbital chemical plants to produce novel or enhanced medicines that can be sent back to the planet's surface," he added.
Dr. Bailet and his team are currently seeking funding to facilitate the first demonstration of their technology in space.